BioCube cell & gene therapy suite for RoslinCT - GMP Grades B, C & D
Connect 2 Cleanrooms was appointed to deliver a GMP classified cleanroom facility and training laboratory for RoslinCT in Edinburgh’s BioQuarter in Scotland.

Key features of the cleanroom
GMP classified manufacturing facility
For cell and gene therapy products
33 rooms
3no. Clean Rooms (Grade B), 2no. Clean Rooms (Grade C)
CFD study & 3D point cloud survey
To plot airflow throughout the building
Principal contractor
Construction was undertaken during the COVID-19 pandemic
Gallery
GMP classified manufacturing facility
RoslinCT has opened its new state-of-the-art ATMP manufacturing facility. The BioCube is designed for clinical and commercially approved cell and gene therapy products and significantly increases its capacity to deliver life-changing therapies for customers and patients.
Connect 2 Cleanrooms was appointed to deliver the GMP classified manufacturing facility and training laboratory for RoslinCT in Edinburgh’s BioQuarter. The proposed works included alterations and fit-outs to an existing 2-storey building to create a modern 33-room manufacturing facility.
- 3no. Clean Rooms (Grade B)
- 2no. Clean Rooms (Grade C)
- 15no. Corridor, Lobby, and Changing Areas (Grades B / C / D)
- Sample and packing area, Cryostore and Vaporized hydrogen peroxide (VHP) staging area (CNC)
- Waste Room, warehouse, and plant room
- Stairwells, foyers, and toilets
- Offices and meeting rooms
- First-floor training laboratory
Features of the new cell & gene therapy suite include cryo storage, medical gas supplies, Vapourised Hydrogen Peroxide (VHP) hatches—for the full kill of microorganisms during materials transfer—and a 21 CFR 11 Environmental Monitoring System that continuously audits the environment to prove GMP-compliancy.
Design and project management
The planning and installation process was fully project managed by Connect 2 Cleanrooms at every stage—from the initial CAD drawings to completion. This included management of the planning and building warrant under Scottish planning regulations.
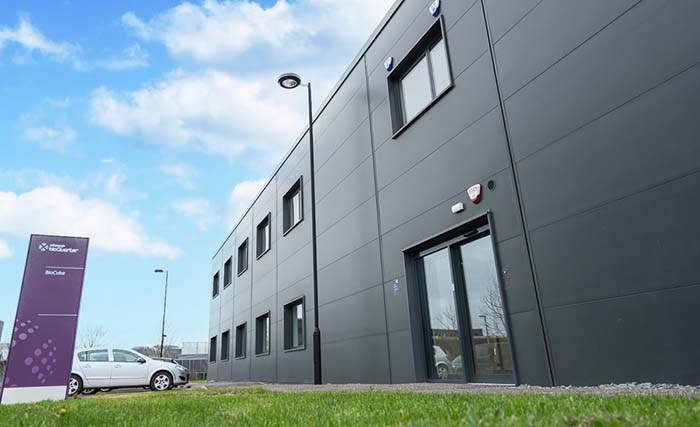
The cleanroom design achieves space efficiency by using the latest decentralised air-handling technology. Connect 2 Cleanrooms created a Computational Fluid Dynamic study to plot airflow throughout the building and used 3D point cloud surveys to plan HVAC ducting, gas lines, interlocks, and raceways. Through this innovative planning of services, office premises were retained in the new facility for RoslinCT.
The decentralised air handling design not only saves space but also enables RoslinCT to perform maintenance in individual rooms without closing the full facility. Along with 24/7 controlled systems and a permanent generator, this ensures continuity of work, which is vital when running clinical trials.
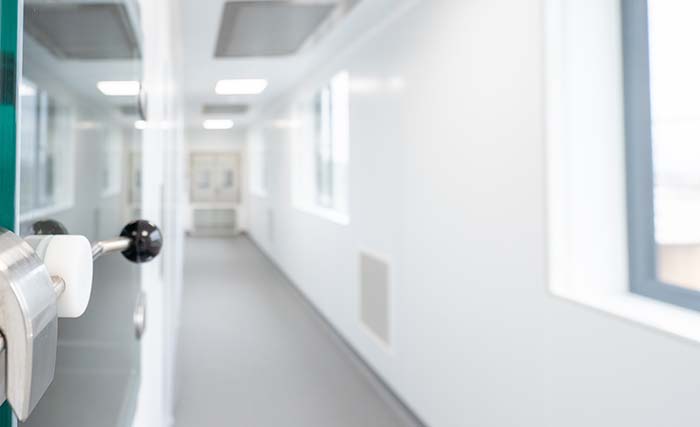
Construction was undertaken during the COVID-19 pandemic and was managed through a Connect 2 Cleanrooms’s in-house installation and validation team, with its network of expert supply partners installing the specialist elements of the built environment. An extensive programme schedule and on-site organisation facilitated multiple teams working on the build and kept teams physically distant to remain COVID-secure.
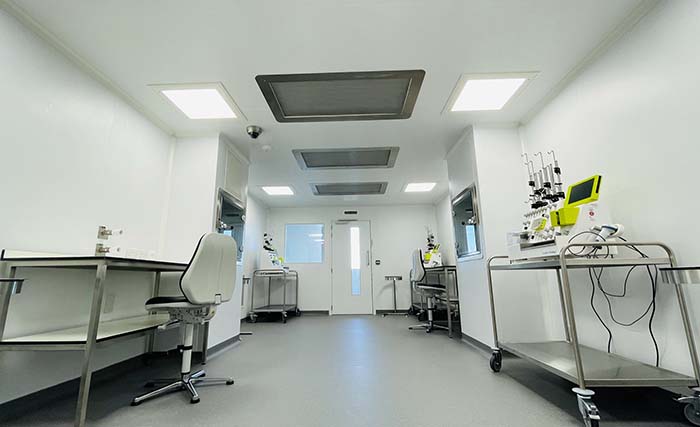
Full GMP qualification
GMP guidelines were followed during the construction of the new facility to ensure all relevant validation and commissioning protocols met regulatory requirements. The facility operates to US and EU GMP standards and ensures the highest standards for the end product.
An extensive Functional Design Specification (FDS)—coupled with specific Project Design submission drawings and schedules—formed Connect 2 Cleanrooms’s proposal and was the cornerstone for the project.
The qualification protocol was reviewed and agreed upon by a validation steering group containing specialists from both Connect 2 Cleanrooms and RoslinCT. To ensure alignment of preparation, review, and execution between Connect 2 Cleanrooms and RoslinCT, a full review structure was implemented for the verification and qualification programme from Design Qualification to Operational Qualification. This review structure meant all acceptance criteria were met and associated non-conformances were mitigated, or where they needed to be recorded were closed promptly.
Connect 2 Cleanrooms testimonial
In the documentation, each test was detailed, the specification for each test was included, and evidence was provided that each test had been completed in line with the specified standard and protocol. Over 1,500 verification tasks were carried out, with RoslinCT witnessing and verifying the testing on most systems.
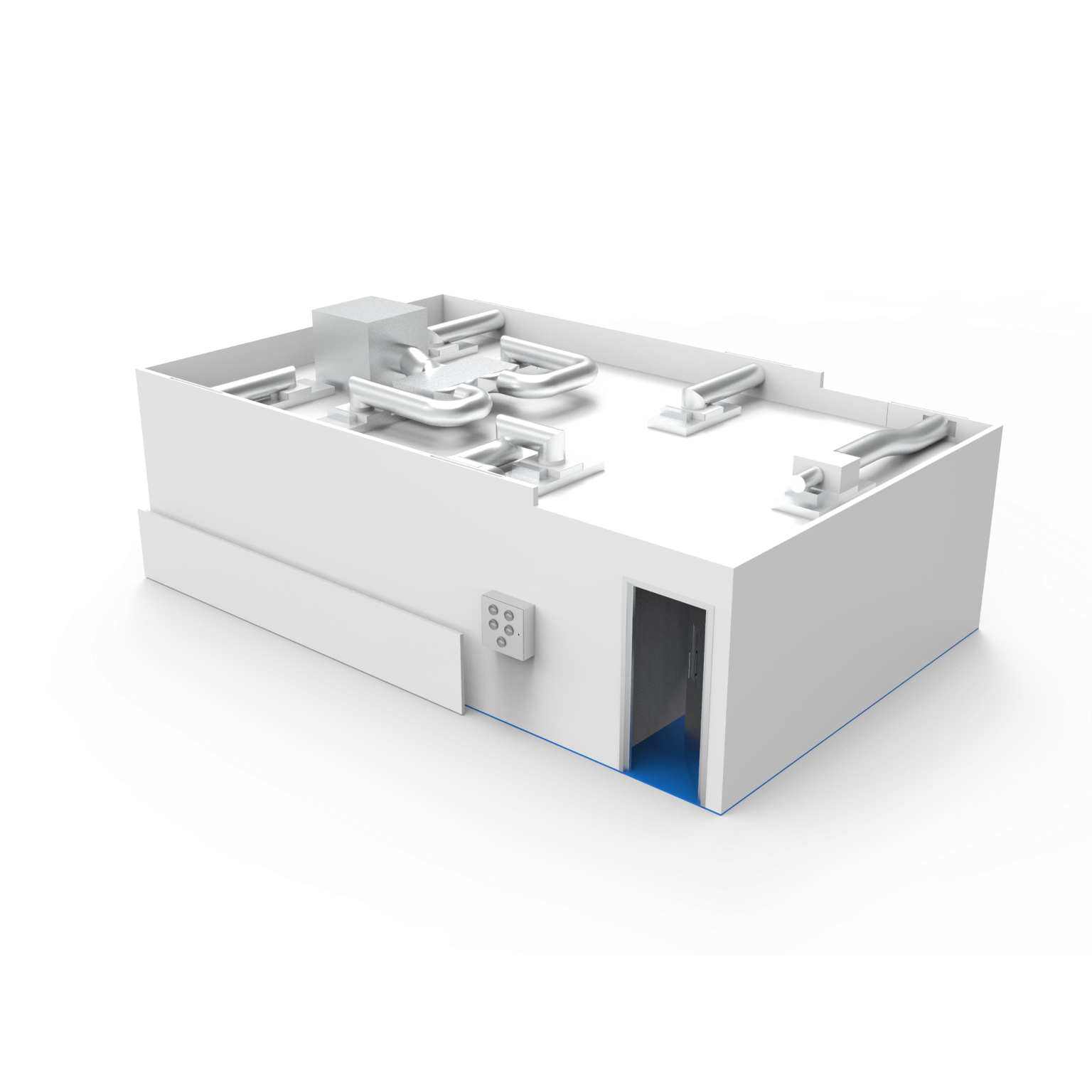
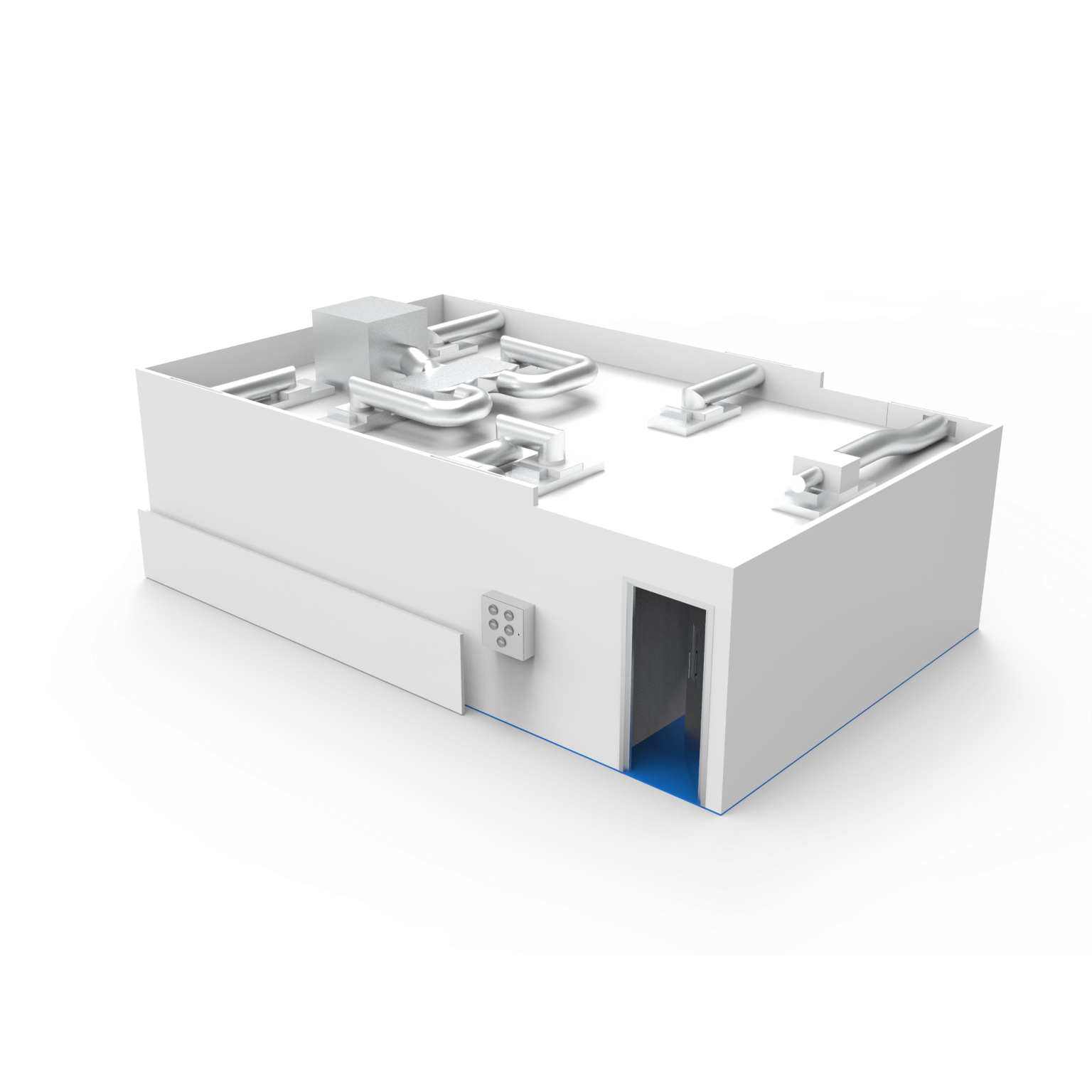
Start a project with us
Our design and build specialists have experience working with customers in all kinds of industries on a global scale, achieving great results time and time again. We’d love to work with you as well!